In the realm of workplace safety, forklift and pallet jack certification stand as crucial pillars. The urgency for these certifications is underscored by alarming statistics: over 100 fatalities and 36,000 serious injuries annually stem from forklift accidents alone. These incidents can lead to hospitalizations or worse, emphasizing the paramount need for proper training and compliance. Safety and adherence to regulations are not mere options but absolute necessities in safeguarding employees’ well-being.
Importance of Certification
Legal Requirements
When it comes to forklift and pallet jack certification, there are specific legal requirements that must be met to ensure workplace safety. OSHA Regulations mandate that all operators of forklifts and pallet jacks must be certified to operate this equipment safely. Failure to comply with these regulations can result in severe consequences, including fines and legal penalties. Additionally, Federal Laws outline the importance of proper training and certification for forklift and pallet jack operators to prevent accidents and ensure a safe working environment.
Safety and Accident Prevention
Certification plays a vital role in reducing workplace injuries related to forklift and pallet jack operations. By ensuring that operators are trained and certified, employers can significantly decrease the risk of accidents occurring in the workplace. Moreover, enhancing operational efficiency is another crucial aspect of certification. Certified operators are more proficient in handling forklifts and pallet jacks, leading to smoother operations and increased productivity.
Employer Responsibilities
Employers have a significant responsibility when it comes to forklift and pallet jack certification. Providing training is not just a recommendation but a legal requirement to ensure the safety of employees. Employers must invest in comprehensive training programs that cover all aspects of forklift and pallet jack operation. Furthermore, ensuring compliance with OSHA regulations is essential. Employers must regularly assess their certification programs to guarantee that they meet all necessary standards.
Training and Safety Procedures
Certification Process
Certification is a critical step in ensuring workplace safety for forklift and pallet jack operators. Proper training is essential to prevent accidents in the workplace. Initial Training provides operators with the necessary skills to handle forklifts and pallet jacks safely. This training covers fundamental operating procedures, safety protocols, and emergency responses. It equips operators with the knowledge needed to navigate potential hazards effectively.
To maintain proficiency and stay updated on best practices, Refresher Courses are recommended for all certified operators. These courses serve as reminders of safety procedures and help reinforce good habits. Regular training sessions ensure that operators remain vigilant and competent in their roles. By investing in ongoing education, employers demonstrate their commitment to upholding high safety standards in the workplace.
Safety Protocols
Handling Equipment Safely is a core aspect of forklift and pallet jack operations. Operators must adhere to strict guidelines when maneuvering these machines to prevent accidents. Safe handling practices include proper load distribution, controlled acceleration and deceleration, and maintaining clear visibility while operating the equipment. By following these protocols diligently, operators can minimize risks and create a secure working environment.
In the event of emergencies, knowing Emergency Procedures is crucial for swift and effective responses. Operators should be trained on how to react to different emergency scenarios such as equipment malfunctions or workplace accidents. Clear communication channels, designated emergency exits, and first-aid protocols should be established to ensure a coordinated response during unforeseen circumstances.
Regular Evaluations
Continuous improvement is key to maintaining a high standard of safety in the workplace. Performance Assessments allow employers to evaluate an operator’s competency level and identify areas for improvement. These assessments provide valuable feedback on an operator’s adherence to safety protocols, efficiency in handling equipment, and responsiveness in emergency situations.
To enhance skills and address any gaps in knowledge, Skill Refreshers are essential components of ongoing training programs. These refreshers focus on reinforcing critical competencies related to forklift and pallet jack operations. By conducting regular skill assessments and providing targeted refresher sessions, employers can ensure that their operators remain proficient in their roles.
Compliance and Inspections
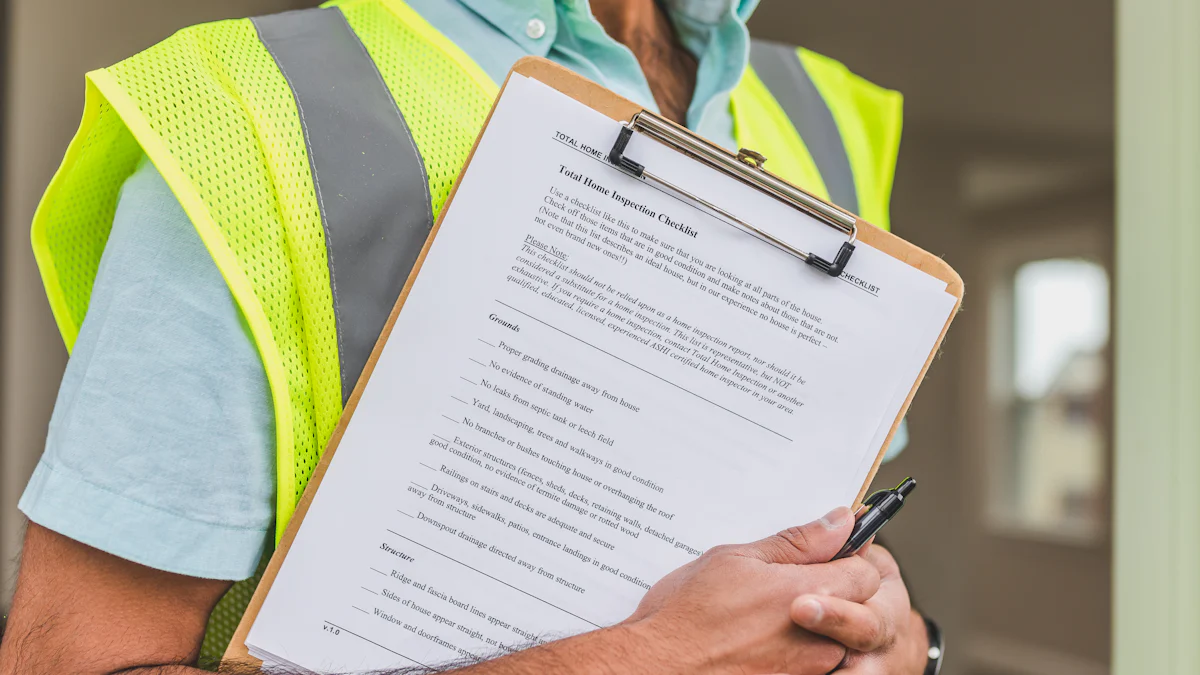
Regular Inspections
Regular inspections are a cornerstone of workplace safety, ensuring that forklifts and pallet jacks are in optimal condition for operation. These inspections serve as proactive measures to identify potential issues before they escalate into safety hazards. By conducting inspection frequency checks at regular intervals, employers can uphold a culture of safety and prevent accidents in the workplace.
- Implement a structured inspection schedule to assess the overall condition of forklifts and pallet jacks.
- Conduct thorough examinations of key components such as brakes, steering mechanisms, and lifting mechanisms.
- Document inspection findings systematically to track maintenance needs and ensure timely repairs.
- Prioritize immediate action on any identified safety concerns to mitigate risks effectively.
In addition to routine inspections, maintenance checks play a vital role in prolonging the lifespan of equipment and safeguarding operators. Regular maintenance not only enhances operational efficiency but also minimizes downtime due to unexpected breakdowns. Employers should establish clear protocols for maintenance checks to promote equipment reliability and longevity.
- Schedule routine maintenance tasks based on manufacturer recommendations and usage patterns.
- Engage qualified technicians to perform detailed inspections and address mechanical issues promptly.
- Keep comprehensive records of maintenance activities, including parts replacements and repairs.
- Invest in quality spare parts and components to maintain equipment performance at optimal levels.
Record Keeping
Documentation requirements are crucial aspects of compliance with regulatory standards governing forklift and pallet jack operations. Accurate record keeping ensures transparency, accountability, and traceability in maintaining equipment safety. By adhering to documentation requirements, employers demonstrate their commitment to upholding industry best practices and legal obligations.
Documentation Requirements:
- Maintain detailed records of operator certifications, training sessions, and competency assessments.
- Document all inspection reports, maintenance logs, and repair histories for audit purposes.
- Store documentation in secure databases or physical files accessible for regulatory reviews.
- Regularly update records to reflect the most recent training initiatives, inspections, or maintenance activities.
Compliance Audits
Conducting compliance audits is essential for evaluating the effectiveness of certification programs and operational procedures related to forklifts and pallet jacks. Audits provide insights into areas needing improvement or adjustment to align with regulatory requirements fully.
- Schedule periodic compliance audits conducted by internal or external auditors with expertise in workplace safety regulations.
- Review documentation thoroughly during audits to verify compliance with OSHA standards and federal laws.
- Implement corrective actions promptly based on audit findings to address non-compliance issues effectively.
- Foster a culture of continuous improvement by integrating audit recommendations into operational practices.
Consequences of Non-Compliance
Non-compliance with certification requirements poses significant risks both legally and operationally. Failure to adhere to regulatory standards can result in severe consequences that impact employee safety, organizational reputation, and financial stability. Understanding the consequences of non-compliance underscores the critical importance of prioritizing certification programs within workplaces.
Legal Penalties:
Violations related to forklift or pallet jack operations can lead to substantial fines imposed by regulatory authorities. Non-compliance with OSHA regulations may result in financial penalties that significantly impact business operations. By complying with certification mandates, employers avoid costly legal repercussions while fostering a safe work environment.
Safety Risks:
Neglecting certification requirements increases the likelihood of workplace accidents caused by inexperienced or untrained operators handling forklifts or pallet jacks improperly. Safety risks associated with non-compliance include injuries, property damage, or even fatalities resulting from preventable incidents. Prioritizing certification mitigates these risks proactively while promoting a culture of safety awareness among employees.
Benefits of forklift certification for employers:
- John Chisholm, an expert in forklift safety, advocates for employee certification to mitigate risks and ensure workplace safety.
- Employers can save costs by investing in certified forklift operators, reducing injuries and liabilities significantly.
By prioritizing certification programs, employers uphold safety standards, avoid legal consequences, and foster a secure work environment. Continuous training and compliance are essential pillars in safeguarding both employees and businesses from potential risks. Strengthening certification protocols not only enhances operational efficiency but also underscores a commitment to excellence in workplace safety.
Post time: Jun-03-2024