Efficient warehouse operations are crucial for productivity and safety. Understanding the role of Pallet Jacks in streamlining tasks is essential. This blog aims to provide valuable insights into maximizing the use of these tools. By exploring their components and functions, readers can enhance their warehouse practices and minimize risks associated with manual handling.
1. Understand the Basics of Hand Cart Forklifts
When delving into the realm of hand cart forklifts, it’s imperative to grasp the intricate details that make up these essential tools for warehouse operations.
Hand Cart Forklift Components
The forks and carriage are fundamental components of a hand cart forklift. The forks, typically made of durable steel, serve as the support structure for lifting loads. They are designed to slide under pallets or heavy items, providing stability during transport. The carriage, located at the front of the forklift, secures the forks in place and ensures that the load remains intact while in motion.
A crucial feature of hand cart forklifts is the hand-crank winch. This mechanism allows operators to lift and lower loads with precision and control. By simply turning the handle, the winch engages, raising or lowering the forks as needed. The reversible handle enables seamless operation in both directions, enhancing efficiency during tasks.
Types of Hand Cart Forklifts
Manual vs. Powered
Hand cart forklifts come in two primary variants: manual and powered. Manual models rely on human effort to operate, making them suitable for lighter loads and smaller warehouses. On the other hand, powered hand cart forklifts utilize electric or hydraulic systems to lift heavier items with ease, ideal for larger warehouses with substantial inventory movement requirements.
Hydraulic Systems
One distinguishing feature among hand cart forklifts is their hydraulic systems. These systems play a vital role in lifting heavy loads efficiently while minimizing strain on operators. Whether it’s a two-wheel or four-wheel model, hydraulic lift mechanisms ensure smooth and controlled movement within warehouse settings.
By understanding these key components and variations in hand cart forklift designs, warehouse personnel can make informed decisions regarding their operational needs.
2. Proper Training and Safety Measures
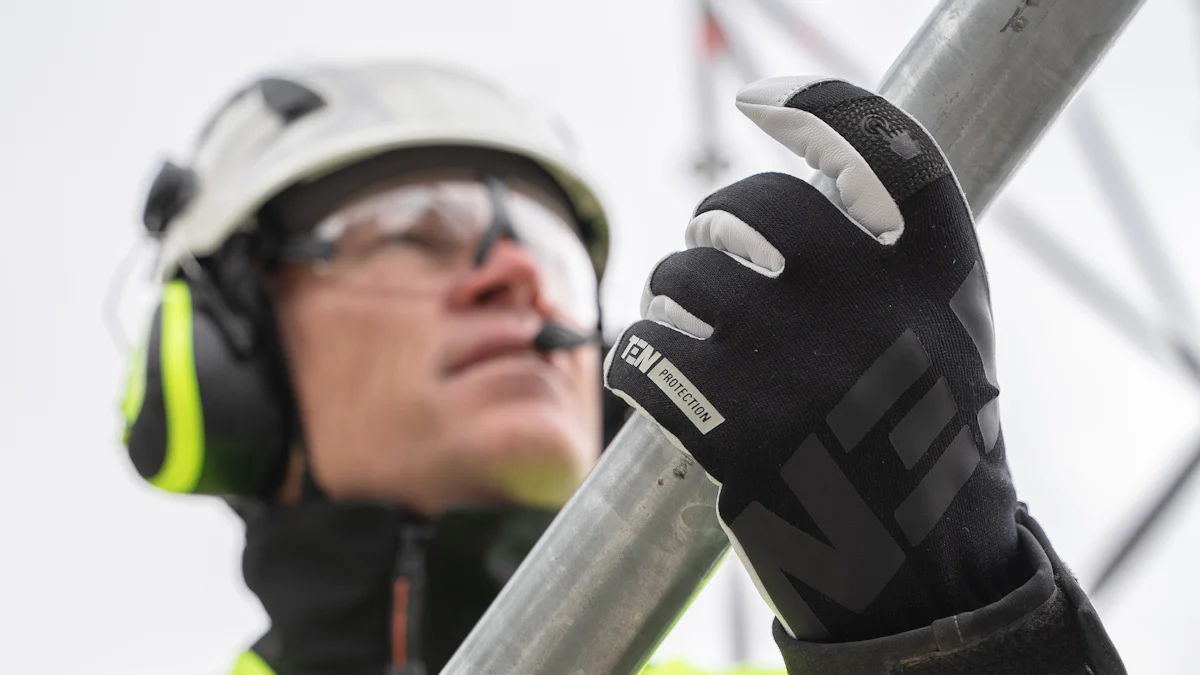
Training Programs
When it comes to operating hand cart forklifts, certification requirements play a crucial role in ensuring the safety and efficiency of warehouse operations. Obtaining proper certification demonstrates that operators have undergone necessary training to handle these tools effectively. By completing certification programs, individuals gain valuable knowledge about the operation, maintenance, and safety protocols associated with hand cart forklifts.
Hands-On Training
Hands-on training is an essential component of mastering the skills needed to operate hand cart forklifts proficiently. Through practical experience, operators can familiarize themselves with the controls, functions, and limitations of these tools. Hands-on training sessions provide a platform for individuals to practice safe handling techniques, understand load capacities, and navigate various warehouse scenarios effectively.
Safety Protocols
Load Limits
Understanding load limits is paramount when using hand cart forklifts in warehouse environments. Exceeding the specified weight capacity can lead to accidents, equipment damage, and potential injuries. By adhering to load limits outlined by manufacturers, operators can prevent overloading situations and maintain a safe working environment. Regular checks on load weights ensure that operations remain within safe parameters.
Safe Handling Techniques
Implementing safe handling techniques is essential for mitigating risks associated with operating hand cart forklifts. Proper lifting procedures, secure positioning of loads, and strategic maneuvering are key aspects of ensuring workplace safety. Operators should be trained to assess load stability, avoid sudden movements that may destabilize the equipment, and prioritize their well-being along with the protection of warehouse inventory.
“Proper Steps and Protocols for Forklift Tire Inspection and Replacement” emphasizes the importance of following correct inspection procedures to enhance operational safety. By conducting regular tire inspections on hand cart forklifts, operators can identify potential issues early on and address them promptly.
3. Maintenance and Inspection
Regular Maintenance
Lubrication
Proper lubrication is essential for the hand cart forklift to function smoothly and efficiently. Regularly applying lubricants to the moving parts reduces friction, preventing wear and tear on components. This maintenance task ensures that the forks and winch operate seamlessly during lifting and lowering operations, enhancing overall performance.
Parts Replacement
Scheduled parts replacement is a critical aspect of maintaining the longevity of a hand cart forklift. Over time, components such as bearings, seals, or hydraulic hoses may wear out due to continuous use. By adhering to a replacement schedule based on manufacturer recommendations, operators can prevent unexpected breakdowns and maintain optimal functionality.
Inspection Checklists
Daily Inspections
Conducting daily inspections is a proactive approach to identifying potential issues before they escalate into major problems. Operators should visually inspect the hand cart forklift for any signs of damage, leaks, or loose connections at the beginning of each shift. Checking the functionality of controls, brakes, and safety features ensures safe operation throughout the workday.
Monthly Inspections
Monthly inspections involve a more thorough assessment of the hand cart forklift’s condition and performance. During these inspections, operators should examine critical components in detail, such as the hydraulic system, electrical connections, and structural integrity. Addressing any minor concerns promptly can prevent costly repairs or downtime in warehouse operations.
Proper maintenance practices are crucial in ensuring workplace safety and operational efficiency. Neglecting routine lubrication or overlooking parts replacement schedules can lead to equipment malfunctions or accidents within warehouse environments.
By prioritizing regular maintenance tasks like lubrication and parts replacement, along with diligent daily and monthly inspections, operators can uphold the reliability and performance of hand cart forklifts in warehouse settings.
4. Efficient Loading and Unloading Techniques
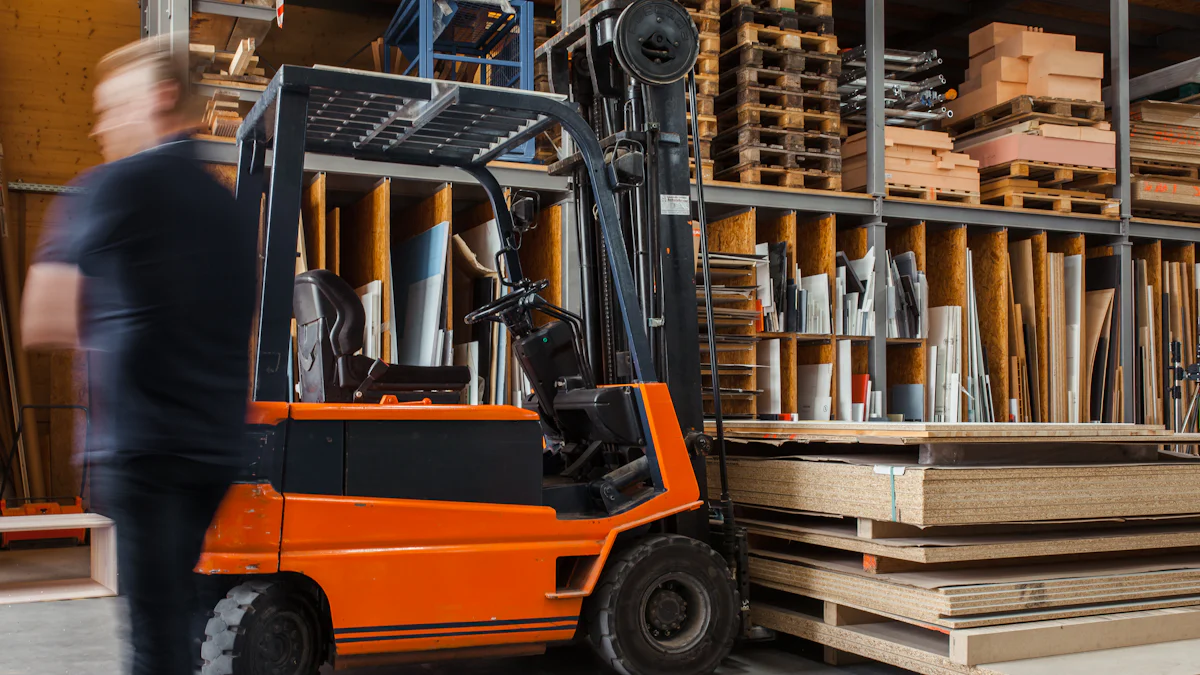
Positioning the Forklift
To ensure optimal efficiency when using a hand cart forklift, operators must master the art of aligning with loads and adjusting fork height accurately.
Aligning with Loads
When aligning with loads, precision is key. By positioning the forklift directly in front of the load, operators can minimize handling time and maximize productivity. Ensuring that the forks are aligned with the edges of the pallet or item guarantees a secure grip during lifting and transport. This meticulous approach not only streamlines operations but also reduces the risk of accidents or damage to warehouse inventory.
Adjusting Fork Height
Adjusting fork height is a critical step in optimizing loading and unloading processes. Operators should raise or lower the forks to match the height of the load, allowing for seamless insertion or extraction. Maintaining proper fork height prevents unnecessary strain on both the equipment and the operator, promoting safe and efficient handling practices. By mastering this technique, warehouse personnel can expedite tasks while maintaining a high level of precision.
Handling Different Load Types
Versatility in handling different load types is essential for adapting to diverse warehouse requirements efficiently.
Pallets
When dealing with pallets, operators should focus on strategic placement and secure handling. By sliding the forks beneath the pallet, ensuring they are centered for balanced support, and lifting smoothly without sudden movements, operators can transport palletized goods with ease. Implementing proper pallet handling techniques minimizes risks such as load shifting or instability during transit, enhancing overall operational safety.
Individual Items
For individual items, attention to detail is paramount. Operators must assess weight distribution, size, and fragility when maneuvering single items using a hand cart forklift. Securely gripping each item with precision, avoiding abrupt movements, and maintaining control throughout the handling process are crucial steps in preventing accidents or damage. Adapting handling techniques based on individual item characteristics ensures efficient movement within warehouse spaces while safeguarding valuable inventory.
Efficient loading and unloading techniques not only optimize workflow but also contribute to a safe working environment in warehouses by reducing operational risks associated with manual material handling practices.
5. Optimizing Warehouse Layout for Hand Cart Forklifts
Aisle Width and Layout
When considering aisle width and layout in warehouse design, it is crucial to tailor these aspects to the specific requirements of hand cart forklift operations.
Narrow Aisles
In warehouses with narrow aisles, maximizing space utilization while ensuring maneuverability for hand cart forklifts is essential. By strategically planning aisle widths, operators can navigate tight spaces efficiently without compromising safety or productivity. Implementing narrow aisles allows for increased storage capacity within the same square footage, optimizing warehouse layout for streamlined operations.
Wide Aisles
Conversely, wide aisles offer advantages in terms of accessibility and flexibility for hand cart forklift movements. With ample space to maneuver and turn, operators can transport loads with ease and precision. Wide aisles accommodate larger turning radii, enabling efficient handling of bulky or oversized items. By incorporating wide aisles into the warehouse layout, organizations can enhance operational flow and minimize congestion during loading and unloading activities.
Storage Solutions
Efficient storage solutions are integral to supporting the functionality of hand cart forklifts within warehouse environments.
Racking Systems
Racking systems play a pivotal role in organizing inventory and optimizing space utilization. By utilizing various racking configurations such as selective pallet racks, drive-in racks, or push-back racks, warehouses can accommodate different load types efficiently. Selective pallet racks provide easy access to individual pallets, while drive-in racks maximize storage density by allowing deep stacking of pallets. Push-back racks offer a dynamic storage solution that facilitates first-in-last-out (FILO) inventory management, enhancing workflow efficiency.
Floor Storage
In addition to vertical storage solutions, floor storage areas are essential for accommodating non-palletized items or bulk goods. Floor storage zones enable quick access to products that do not require shelving or racking systems. By delineating designated floor storage areas based on product categories or frequency of use, warehouses can streamline picking processes and facilitate seamless replenishment tasks. Implementing efficient floor storage strategies ensures that hand cart forklift operators can easily locate and retrieve items during daily operations.
“Optimizing warehouse layout is a strategic approach to enhancing operational efficiency and maximizing available space.” By customizing aisle widths according to hand cart forklift requirements and implementing versatile storage solutions like racking systems and floor storage areas, warehouses can create an environment conducive to smooth material handling processes.
By aligning aisle width considerations with hand cart forklift specifications and integrating diverse storage solutions tailored to inventory needs, organizations can optimize their warehouse layouts effectively.
- To ensure efficient warehouse operations, it is imperative to prioritize safety measures and continuous improvement. Following strict guidelines and safety procedures can prevent incidents that lead to injuries and damage. Proper maintenance and inspection of forklifts are essential to prevent accidents like tip-overs and collapses. By emphasizing the importance of ongoing training, meticulous maintenance, and strategic layout planning, warehouses can enhance productivity while safeguarding personnel and inventory. Future considerations should focus on implementing advanced technologies and ergonomic solutions to further optimize operational workflows.
Post time: Jun-07-2024