Maintaining electric scissor lift pallet jacks is paramount for their longevity and efficient operation. By following key maintenance tips, such as regular lubrication and thorough cleaning, operators can prevent accidents and ensure optimal performance. The benefits of consistent upkeep include extended equipment life, reduced downtime, and significant cost savings. Prioritizing maintenance not only enhances safety but also maximizes the efficiency of these essential tools.
Importance of Regular Maintenance
When it comes to electric scissor lift pallet jacks maintenance, prioritizing regular upkeep is crucial for ensuring safety, efficiency, and longevity. Let’s delve into the significance of maintaining these essential tools through a proactive approach.
Safety
To begin with, focusing on maintenance plays a pivotal role in preventing accidents. By adhering to a structured maintenance schedule, operators can identify and address potential issues before they escalate into safety hazards. Regular inspections and upkeep not only safeguard the well-being of individuals operating the equipment but also create a secure work environment for everyone involved.
Ensuring operator safety is another key aspect influenced by regular maintenance practices. By conducting routine checks and servicing, operators can feel confident in the reliability of the pallet jack during operation. This instills a sense of trust in the equipment’s performance, ultimately enhancing operator confidence and reducing the likelihood of accidents or malfunctions.
Efficiency
Maintenance directly contributes to reducing downtime, a critical factor in maximizing operational efficiency. When electric scissor lift pallet jacks are well-maintained, they are less prone to unexpected breakdowns or malfunctions that could halt productivity. By incorporating regular maintenance tasks into daily operations, businesses can streamline their workflow and minimize disruptions caused by equipment failures.
Furthermore, proper maintenance leads to enhanced performance of electric scissor lift pallet jacks. Well-lubricated wheels and axles ensure smooth movement and maneuverability, allowing operators to navigate various work environments with ease. Consistent cleaning practices also contribute to optimal performance by removing dust and debris that could hinder the jack’s functionality.
Longevity
Extending the equipment life of electric scissor lift pallet jacks is a significant benefit of regular maintenance efforts. By following manufacturer-recommended maintenance procedures and addressing any issues promptly, operators can prolong the lifespan of these valuable assets. This not only maximizes the return on investment but also reduces the frequency of replacements or repairs, saving both time and money in the long run.
Moreover, prioritizing maintenance translates into substantial cost savings for businesses. By proactively caring for electric scissor lift pallet jacks, companies can avoid costly repairs resulting from neglected maintenance issues. Additionally, efficient equipment operates at peak performance levels, consuming less energy and minimizing operational costs over time.
Monthly Maintenance Tasks
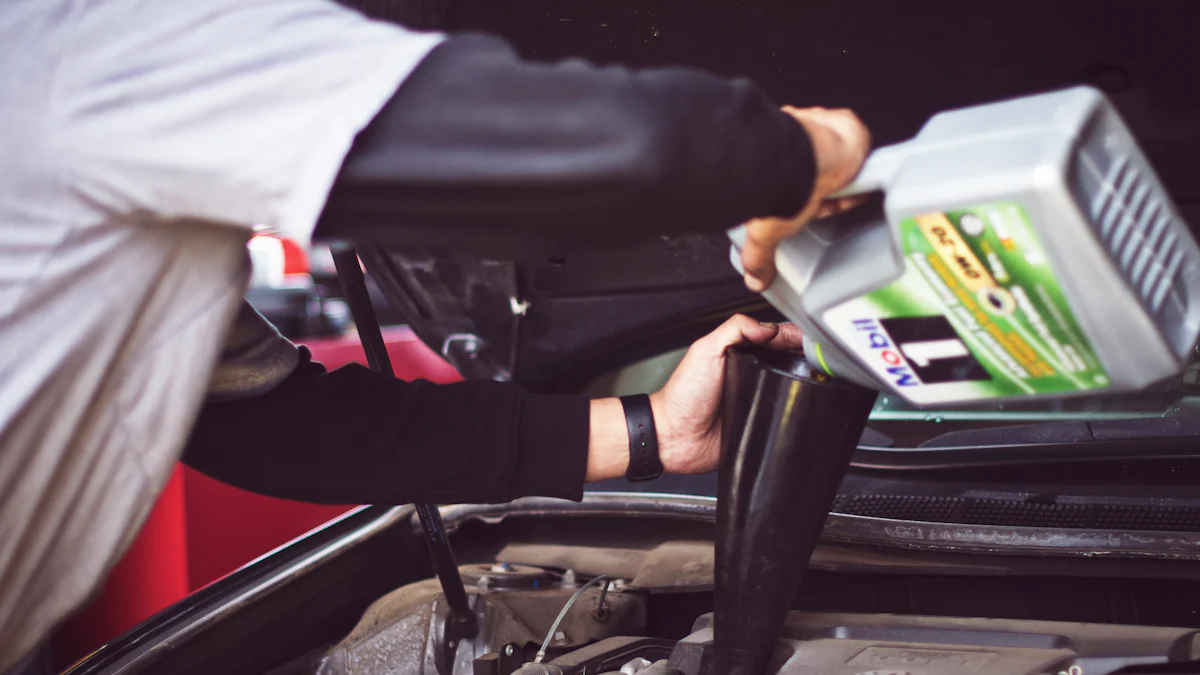
Lubrication
When it comes to maintaining electric scissor lift pallet jacks, prioritizing regular lubrication is essential for ensuring optimal performance and longevity. By applying long-life grease to the wheels and axles, operators can guarantee smooth operation and prevent premature wear and tear. Let’s delve into the key aspects of lubricating these critical components.
Wheels and Axles
Lubricating the wheels and axles of an electric scissor lift pallet jack is a fundamental monthly maintenance task that should not be overlooked. By using high-quality grease on these components, operators can minimize friction, reduce noise levels, and extend the lifespan of the equipment. Proper lubrication also promotes efficient movement, allowing the pallet jack to maneuver effortlessly in various work environments.
Grease Fittings
Another crucial aspect of monthly maintenance is tending to the grease fittings of the electric scissor lift pallet jack. These fittings serve as access points for applying grease to specific parts of the equipment’s mechanism. By regularly greasing these fittings, operators ensure that all moving parts operate smoothly without unnecessary strain or resistance. This preventive measure enhances overall performance and prevents potential breakdowns due to inadequate lubrication.
Cleaning
Regular cleaning is a vital component of maintaining electric scissor lift pallet jacks, contributing to their efficiency and longevity. By removing dust and debris from various components, operators can prevent malfunctions and ensure optimal functionality. Let’s explore the significance of cleaning as part of monthly maintenance tasks.
Removing Dust and Debris
Thoroughly cleaning the electric scissor lift pallet jack involves eliminating accumulated dust and debris from its surfaces and mechanisms. Dust particles can impair performance by clogging moving parts or hindering electrical connections. By routinely cleaning these areas, operators safeguard the equipment against potential damage while promoting a safe working environment for all personnel.
Battery Maintenance
In addition to general cleaning, paying attention to battery maintenance is crucial for maximizing the efficiency of an electric scissor lift pallet jack. Regularly inspecting the battery terminals for dirt or corrosion ensures proper electrical conductivity and prolongs battery life. Operators should also check electrolyte levels periodically to prevent issues related to undercharging or overcharging, which could impact overall performance.
Inspection
Conducting thorough inspections is a proactive approach that helps identify potential issues before they escalate into major problems. Regular inspection of key components ensures that the electric scissor lift pallet jack operates safely and efficiently at all times. Let’s explore essential inspection tasks as part of monthly maintenance routines.
Hydraulic Lift
Inspecting the hydraulic lift system is critical for verifying its functionality without any load attached. Operators should test the hydraulic system for smooth operation, checking for leaks or unusual noises that may indicate underlying issues. Maintaining proper hydraulic function is essential for lifting loads safely and efficiently while preventing accidents in the workplace.
Forks and Rollers
Another integral part of monthly maintenance involves inspecting the forks and rollers of the electric scissor lift pallet jack. These components play a significant role in supporting loads during operation; therefore, ensuring their structural integrity is paramount for safety. Operators should look out for any signs of damage, such as cracks or bends, which could compromise load-bearing capacity or stability.
Bi-Annual Maintenance Tasks
Comprehensive Service
Professional Servicing
When it comes to electric scissor lift pallet jacks, professional servicing every six months is a crucial aspect of ensuring optimal performance and longevity. By entrusting the maintenance of these essential tools to certified technicians, operators can address any underlying issues effectively. Professional servicing involves a comprehensive inspection of all components, from the hydraulic system to the electrical connections, to identify potential problems before they escalate. This proactive approach not only enhances safety but also minimizes the risk of unexpected breakdowns during operation.
Detailed Inspection
A detailed inspection as part of bi-annual maintenance tasks is essential for maintaining the reliability of electric scissor lift pallet jacks. Technicians meticulously examine each part of the equipment, checking for wear and tear, loose connections, or signs of damage. By conducting a thorough assessment, operators can address minor issues promptly and prevent them from developing into major malfunctions. This meticulous approach to inspection ensures that the pallet jack operates at peak performance levels, contributing to a safe and efficient work environment.
Fluid Levels
Checking Oil and Coolant
Monitoring oil and coolant levels in electric scissor lift pallet jacks is a critical bi-annual maintenance task that should not be overlooked. Proper levels of oil ensure smooth operation of the machinery’s moving parts, reducing friction and heat generation. Similarly, maintaining adequate coolant levels prevents overheating of essential components, safeguarding the equipment from potential damage. By regularly checking and replenishing oil and coolant levels, operators can prolong the lifespan of their pallet jacks and avoid costly repairs due to inadequate lubrication or cooling.
Hydraulic Fluids
Inspecting hydraulic fluids is another key aspect of bi-annual maintenance for electric scissor lift pallet jacks. The hydraulic system plays a vital role in lifting heavy loads safely and efficiently; therefore, ensuring proper fluid levels is paramount for optimal performance. Technicians assess the condition and quantity of hydraulic fluids, looking for any signs of contamination or leaks that could compromise the system’s functionality. By maintaining clean and adequate hydraulic fluids, operators guarantee smooth operation and prevent potential failures during operation.
Battery Health
Terminal Cleaning
Maintaining battery health is crucial for maximizing the efficiency and lifespan of electric scissor lift pallet jacks’ batteries. One essential bi-annual task is terminal cleaning, where operators remove dirt or corrosion from battery terminals to ensure proper electrical conductivity. Clean terminals facilitate seamless power transmission within the equipment, preventing voltage drops or interruptions during operation. By incorporating terminal cleaning into regular maintenance routines, operators can optimize battery performance and extend its service life effectively.
Electrolyte Levels
Regularly monitoring electrolyte levels in batteries is a preventive measure that contributes to overall equipment reliability. Electrolytes play a significant role in battery function by facilitating chemical reactions that generate power for the pallet jack. Operators should check electrolyte levels periodically and top up as needed to maintain optimal battery performance. Proper electrolyte levels ensure consistent power output during operation, preventing unexpected shutdowns or reduced efficiency due to insufficient electrolytes.
Daily Checks and Cleaning
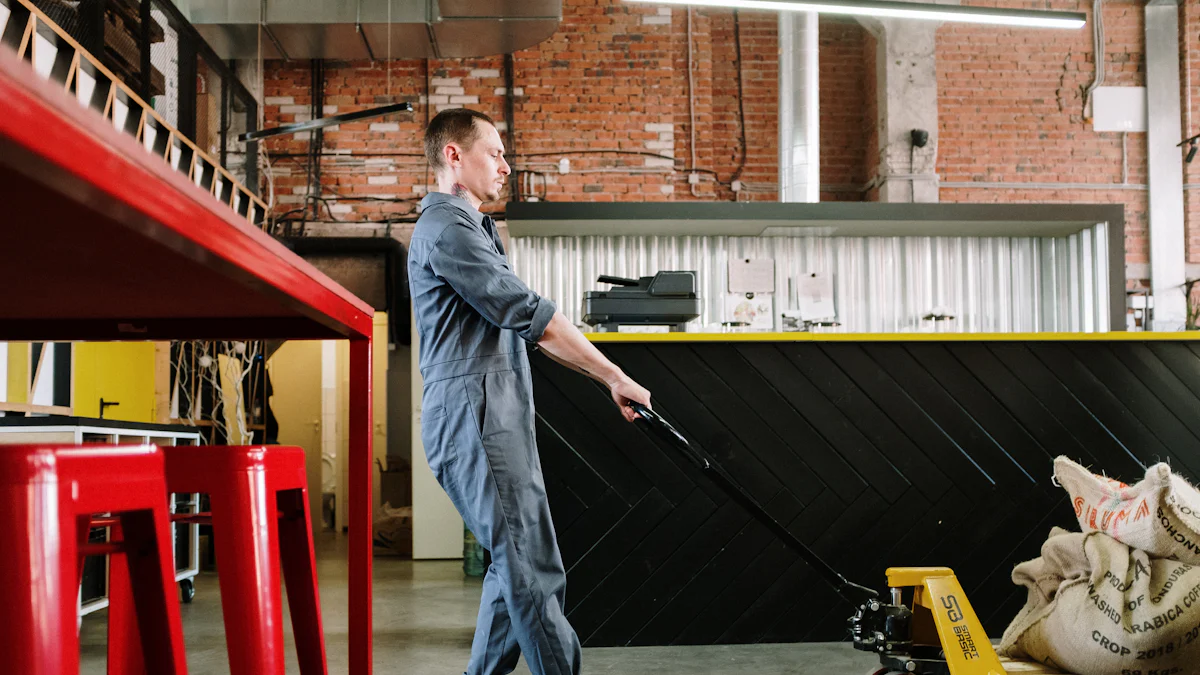
Operator Training
Proper Usage
When operating an electric scissor lift pallet jack, understanding the correct procedures is essential for safe and efficient use. Following the manufacturer’s guidelines on load capacity and operational limits ensures that the equipment functions optimally without risking damage or accidents. By adhering to proper usage protocols, operators can maintain a secure work environment and prevent unnecessary wear on the pallet jack components.
Safety Protocols
Implementing stringent safety protocols during electric scissor lift pallet jack operation is paramount for accident prevention. Operators should undergo comprehensive training on handling the equipment, including emergency procedures and risk mitigation strategies. By prioritizing safety protocols, businesses can minimize workplace incidents and promote a culture of safety awareness among all personnel.
Visual Inspections
Checking for Damage
Regular visual inspections of an electric scissor lift pallet jack are crucial for identifying potential issues before they escalate. Operators should visually assess all components for signs of wear, damage, or misalignment that could compromise the equipment’s performance. By promptly addressing any visible damage, operators can prevent costly repairs and ensure the longevity of the pallet jack.
Ensuring Cleanliness
Maintaining cleanliness in an electric scissor lift pallet jack is more than just aesthetics; it directly impacts performance and longevity. Regular cleaning of surfaces, controls, and moving parts prevents debris buildup that could impede operation or cause malfunctions. By ensuring cleanliness through routine inspections, operators uphold optimal working conditions for the equipment.
Battery Charging
Full Charge Before Use
Prioritizing a full charge before utilizing an electric scissor lift pallet jack is essential for uninterrupted operation. A fully charged battery maximizes performance efficiency and ensures consistent power output during tasks. By adhering to this practice, operators avoid unexpected downtimes due to insufficient battery levels and maintain productivity throughout operations.
Avoiding Overcharging
Preventing overcharging of the battery in an electric scissor lift pallet jack is critical for prolonging its lifespan and maintaining optimal functionality. Overcharging can lead to battery degradation, reduced efficiency, and potential safety hazards. Operators should adhere to recommended charging times and avoid leaving the battery connected unnecessarily to preserve its health and performance.
“At the end of the day, regular inspections and preventive maintenance,
fixing small problems proactively before they become more expensive
and labor-intensive to address play a key role in lower overall repair costs
and reduced downtime over the life of these machines,” Nunez said.
Implementing a preventive maintenance plan for loading dock equipment, such as scissor lifts and dock lifts, offers various benefits. Regular inspections and proactive maintenance not only lower overall repair costs but also reduce downtime significantly. By prioritizing maintenance tasks and addressing issues promptly, operators can ensure the longevity of the equipment, increase efficiency, and create a safer work environment. Encouraging a proactive approach to maintenance is essential for optimal performance and safety in the long run.
Post time: Jun-17-2024