In the realm of material handling, selecting the ideal scissor pallet jack is paramount. These innovative tools, known for their unique elevating mechanism, play a crucial role in enhancing operational efficiency. By enabling operators to lift pallets to a comfortable working height, scissor pallet jacks facilitate seamless transportation and access to goods at elevated levels. This blog will delve into the significance of three essential features that distinguish top-tier scissor pallet jacks, shedding light on their pivotal role in diverse industrial applications.
Load Capacity
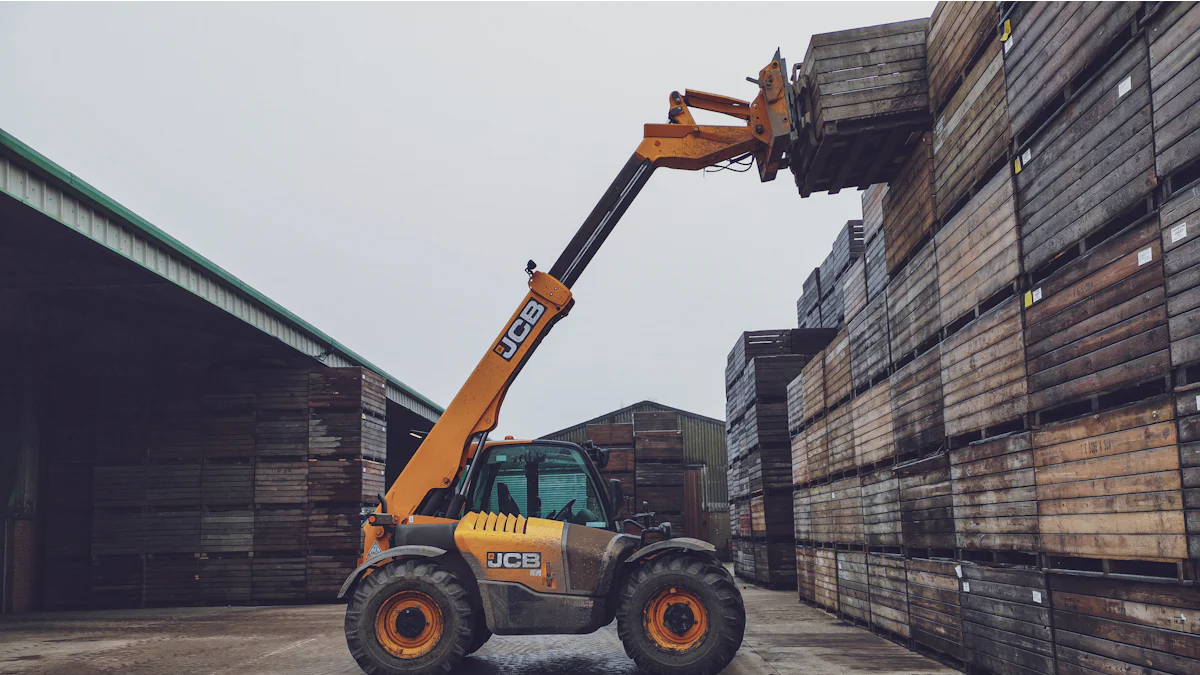
When considering a scissor pallet jack, one of the fundamental aspects to evaluate is its load capacity. The importance of load capacity cannot be overstated, especially in various industrial applications where efficient material handling is crucial. High-capacity scissor pallet jacks, such as the Scissor Lift Pallet Jack and the *Global Industrial™ Industrial Duty Pallet Jack*, offer weight capacities ranging from 2,200 lbs to 5,500 lbs, ensuring they can handle heavy-duty loads with ease.
In industrial applications, where time is of the essence and productivity is key, having a scissor pallet jack with an adequate load capacity is essential. Whether it’s loading/unloading conveyors or feed presses, these high-capacity jacks provide the necessary support for seamless operations. Additionally, they come equipped with stabilizers that keep the jack steady while lifting loads to higher spaces, enhancing both safety and efficiency.
When it comes to safety considerations, choosing a scissor pallet jack with the right load capacity plays a critical role in preventing accidents and injuries. Overloading a pallet jack beyond its capacity can lead to instability and potential hazards in the workplace. By selecting a high-capacity jack like the Toyota Tora-Max 2TWB33 Electric Pallet Jack, operators can ensure that they stay within safe weight limits while maximizing their lifting capabilities.
Selecting the right load capacity involves evaluating several factors to meet specific operational requirements. Factors such as the type of materials being handled, frequency of use, and maximum weight limits need to be taken into account when choosing a scissor pallet jack. Understanding these factors allows businesses to select a suitable load capacity that aligns with their unique needs.
Commonly available load capacities for high-capacity scissor pallet jacks range from 2,200 lbs to 3,300 lbs. Models like High Lift Pallet Jacks offer versatile options for different industrial settings by providing varying weight capacities tailored to specific applications. By opting for a scissor pallet jack with an appropriate load capacity, businesses can optimize their material handling processes efficiently.
Raised Fork Height
Benefits of Optimal Fork Height
Raised fork height is a critical feature in scissor pallet jacks that offers numerous advantages for operators and businesses. By ensuring the forks can reach an optimal height, operators can experience enhanced ergonomic advantages during material handling tasks. The ability to adjust the fork height to a comfortable level reduces strain on the body, particularly on the back and shoulders. This ergonomic design promotes better posture and minimizes the risk of musculoskeletal injuries, contributing to a safer working environment.
Moreover, achieving the optimal fork height leads to improved operational efficiency within industrial settings. With the forks positioned at the right elevation, operators can swiftly load and unload pallets without unnecessary bending or stretching. This streamlined process not only enhances productivity but also reduces the time required for material handling tasks. By investing in a scissor pallet jack with adjustable fork heights, businesses can optimize their workflow and ensure seamless operations.
Selecting the Appropriate Fork Height
When it comes to selecting the appropriate fork height for a scissor pallet jack, adhering to industry standards is paramount. Industry regulations outline specific guidelines regarding safe fork heights based on different applications and environments. By following these standards, businesses can guarantee compliance with safety protocols and create a secure working environment for their employees.
Practical examples highlight how choosing the right fork height can significantly impact operational effectiveness. For instance, models like Advantage High-Lift Scissor-Lift Pallet Trucks offer a maximum raised height of 32 inches, surpassing traditional pallet jacks’ capabilities. This extended reach not only improves accessibility to elevated goods but also contributes to injury prevention by reducing strenuous bending and heavy lifting.
In comparison, standard pallet jacks typically have limited raised heights averaging around 8 inches, restricting their versatility in handling various loads efficiently. High lift pallet jacks equipped with advanced hydraulic systems can elevate loads up to 833mm in height without requiring additional equipment like ladders or scaffolding. This innovative feature streamlines material handling processes by eliminating unnecessary steps and enhancing overall productivity.
By considering these practical examples and industry standards when selecting a scissor pallet jack with an appropriate fork height, businesses can optimize their warehouse operations while prioritizing employee safety and well-being.
Ergonomic Design
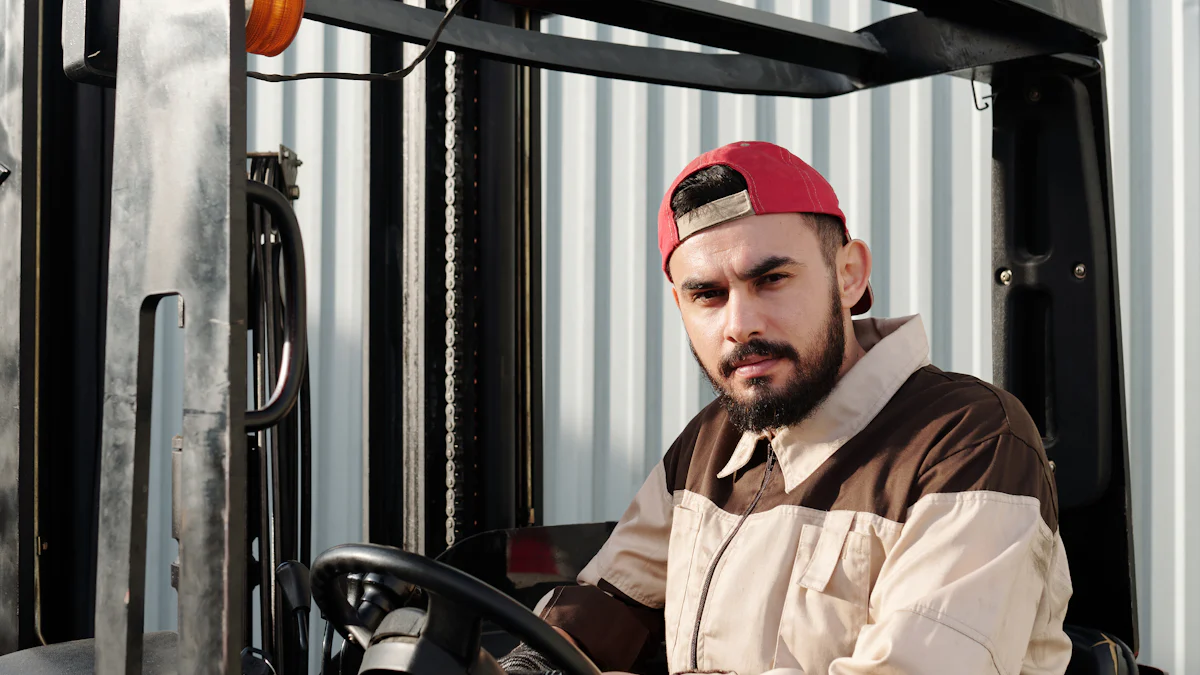
Preventing Injuries
In the realm of material handling, scissor pallet jacks stand out for their innovative combination of a pallet jack and lifting table. This unique design feature plays a crucial role in reducing muscle fatigue and enhancing productivity for operators. By integrating ergonomic elements into the scissor pallet jack’s structure, manufacturers aim to create a tool that not only streamlines material handling processes but also prioritizes operator safety.
When examining the impact of manual pallet jacks on worker safety, it becomes evident that traditional models can lead to musculoskeletal injuries in the workplace. The repetitive strain from manual lifting and maneuvering of heavy loads can result in back pain, shoulder injuries, and other related health issues. To address these concerns, electric pallet jacks have emerged as a safer and more efficient alternative, offering ergonomic benefits that contribute to a healthier work environment.
Common Workplace Injuries
One of the primary advantages of incorporating ergonomic features into scissor pallet jacks is the reduction of common workplace injuries associated with manual material handling tasks. Operators often face risks such as strains, sprains, and overexertion when using traditional equipment. By utilizing scissor pallet jacks with ergonomic designs, businesses can mitigate these risks and create a safer operational environment.
The ergonomic features present in modern scissor pallet jacks are specifically engineered to minimize stress on the body during lifting and transporting activities. These features include adjustable handle heights for improved operator comfort, cushioned grips to reduce hand fatigue, and smooth-rolling wheels for effortless maneuverability. By prioritizing ergonomics in equipment selection, companies demonstrate their commitment to employee well-being while optimizing workflow efficiency.
Musculoskeletal injuries resulting from improper lifting techniques can be significantly reduced by investing in ergonomically designed scissor pallet jacks.
Enhancing Productivity
Design Innovations
Innovative design elements play a pivotal role in enhancing the productivity levels of operators using scissor pallet jacks. Functional benefits such as increased load capacity, extended fork heights, and user-friendly controls contribute to a more efficient material handling process. Manufacturers continue to introduce design innovations that cater to evolving industry needs while focusing on improving overall operational performance.
High lift pallet jacks have been shown to increase productivity by up to 40% compared to traditional models due to their advanced features and capabilities. These innovative tools offer enhanced lifting capacities combined with intuitive controls that streamline workflow processes. By leveraging design innovations in scissor pallet jacks, businesses can achieve higher throughput rates and optimize their warehouse operations effectively.
Case Studies
Functional Benefits of Scissor Lift Pallet Jacks
- Increased Efficiency: Companies adopting scissor lift pallet jacks reported a significant improvement in efficiency metrics.
- Streamlined Operations: The integration of ergonomic design features led to smoother material handling processes.
- Reduced Downtime: Operators experienced fewer instances of fatigue-related delays during daily tasks.
- Enhanced Safety: The ergonomic enhancements resulted in decreased workplace accidents and injuries.
By analyzing these case studies, it becomes evident that investing in high-quality scissor lift pallet jacks with ergonomic designs yields tangible benefits for businesses across various industries.
- To summarize, the three essential features to look for in a scissor pallet jack are high load capacity, optimal fork height, and ergonomic design. These features are crucial for enhancing operational efficiency and ensuring safety in material handling tasks.
- When choosing the right scissor pallet jack, consider reputable brands like Global Industrial™ and Mighty Lift that offer high-quality options with impressive weight capacities. The Global Industrial™ Industrial Duty Pallet Jack stands out with its robust 5500 lb. capacity and smooth operation features, making it ideal for various industrial applications.
- For future considerations, prioritize selecting a scissor pallet jack that not only meets your current needs but also provides room for growth and innovation in your material handling processes. Investing in a reliable and efficient scissor pallet jack is an investment in the productivity and safety of your operations.
Post time: Jun-17-2024