Maintaining a pallet jack is crucial for its longevity and optimal performance. Understanding how to repair a pallet jack can save time and money in the long run. By following simple steps, you can ensure that your equipment operates smoothly. Let’s explore the significance of regular maintenance, the advantages of repairing a pallet jack, and an overview of the repair process.
Step 1: Unload and Prepare
When unloading the pallet jack, it is essential to prioritize safety precautions to prevent any accidents. Begin by ensuring that the area around the pallet jack is clear of obstacles or debris that could hinder the unloading process. This step guarantees a safe environment for both the operator and the equipment.
Next, focus on implementing proper unloading techniques to maintain the integrity of the pallet jack. By following manufacturer guidelines and recommendations, operators can ensure that the unloading process is executed efficiently without causing any damage to the equipment. This approach promotes longevity and optimal performance for the pallet jack.
Moving on to preparing for pumping, operators should start by checking the tow bar for any signs of wear or damage. Inspecting this component regularly allows operators to identify potential issues early on and address them promptly, preventing further complications down the line.
Once the tow bar inspection is complete, it’s time to position the pallet jack correctly for pumping. Proper positioning ensures that the hydraulic system functions effectively during operation, reducing strain on critical components and extending the lifespan of the equipment.
Incorporating these practices into regular maintenance routines enhances operational efficiency and minimizes downtime due to unexpected failures. By prioritizing safety, following proper procedures, and conducting thorough inspections, operators can maintain their pallet jacks in optimal condition for extended periods.
Step 2: Lower and Pump
When operating a pallet jack, it is essential to understand the significance of lowering and pumping techniques. Pallet jacks play a crucial role in various industries, facilitating the movement of heavy loads with ease. By mastering the art of lowering and pumping, operators can ensure the efficient operation of their equipment.
Lower the Pallet Jack
To begin the process, operators should focus on operating the lever effectively. The lever serves as a control mechanism for adjusting the height of the pallet jack. By engaging with the lever in a precise manner, operators can smoothly lower the forks to ground level, preparing them for loading or unloading tasks.
Ensuring proper lowering is vital to prevent any mishaps during operation. By maintaining control over the descent of the pallet jack, operators can avoid sudden drops that may damage both the equipment and the load being transported. This careful approach promotes safety in the workplace and prolongs the lifespan of the pallet jack.
Pump Up the Pallet Jack
Once the pallet jack is appropriately lowered, it’s time to focus on setting the lever to ‘Lower’ for pumping. This setting allows operators to engage with the hydraulic system effectively, enabling them to raise heavy loads effortlessly. By following manufacturer guidelines on lever settings, operators can optimize the lifting capacity of their pallet jacks.
Mastering pumping techniques is essential for smooth operation. Operators should adopt a consistent rhythm while pumping to maintain a steady flow of hydraulic fluid within the system. This technique ensures that sufficient pressure is generated to lift heavy loads without straining the equipment or compromising safety standards.
Step 3: Inspect and Clean

Regular Cleaning
To maintain the optimal functionality of a pallet jack, operators should prioritize regular cleaning practices. This essential task involves removing debris that may accumulate on various components of the equipment, hindering its smooth operation over time.
When removing debris, operators should start by inspecting the forks and wheels for any foreign objects that could impede movement. By systematically clearing away dirt, dust, or other obstructions, operators can ensure that the pallet jack remains in top condition for daily use. Utilizing appropriate cleaning tools such as brushes or compressed air can expedite this process and enhance the overall cleanliness of the equipment.
Inspect Moving Parts
In addition to regular cleaning, inspecting the moving parts of a pallet jack is crucial for identifying potential issues early on. Operators should focus on lubricating parts that experience friction during operation to prevent premature wear and ensure smooth functionality. Applying lubricants to key areas such as hinges, axles, and wheels can significantly extend the lifespan of these components.
Furthermore, checking for wear and tear on moving parts is essential for preemptively addressing any signs of damage or degradation. By visually inspecting critical components like seals, bearings, and hydraulic mechanisms, operators can detect abnormalities that may indicate impending malfunctions. Promptly replacing worn-out parts or scheduling repairs can prevent costly breakdowns and downtime in the future.
Step 4: Drain and Test
Drain the Hydraulic System
To drain the hydraulic system of a pallet jack, operators must follow specific steps to ensure optimal functionality.
Loosening the Screw
Initiate the drainage process by locating the screw that secures the cover over the reservoir. Loosen this screw carefully using an appropriate tool, such as an Allen wrench. By loosening the screw, operators can access the hydraulic fluid within the system for maintenance purposes.
Draining Techniques
After loosening the screw, it is essential to employ effective draining techniques to remove old or contaminated hydraulic fluid. Operators should position a suitable container beneath the drain point to collect the fluid efficiently. By allowing gravity to assist in draining, operators can facilitate a smooth and thorough extraction process. Once all the fluid has been drained, securely tighten the screw back into place to prevent leaks and maintain system integrity.
Test the Operation
Following drainage, it is crucial to test the operation of the pallet jack to verify its functionality post-maintenance.
Checking for Proper Functionality
Operators should conduct a series of tests to ensure that all components are operating correctly after draining and refilling the hydraulic system. By engaging with different functions of the pallet jack, such as lifting and lowering loads, operators can assess whether any issues arise during operation. This step allows operators to identify potential problems early on and address them promptly before they escalate.
Removing Air from the System
If operators encounter issues such as air trapped in the hydraulic system post-drainage, they must take immediate action to resolve this issue effectively. One method involves pumping the handle multiple times without any weight on the forks to expel air bubbles from the system. By removing air pockets through this process, operators can restore proper functionality to their pallet jack and ensure smooth operation during daily tasks.
By adhering to these guidelines for draining and testing a pallet jack’s hydraulic system, operators can maintain their equipment’s performance and longevity effectively.
Step 5: Troubleshoot Common Issues
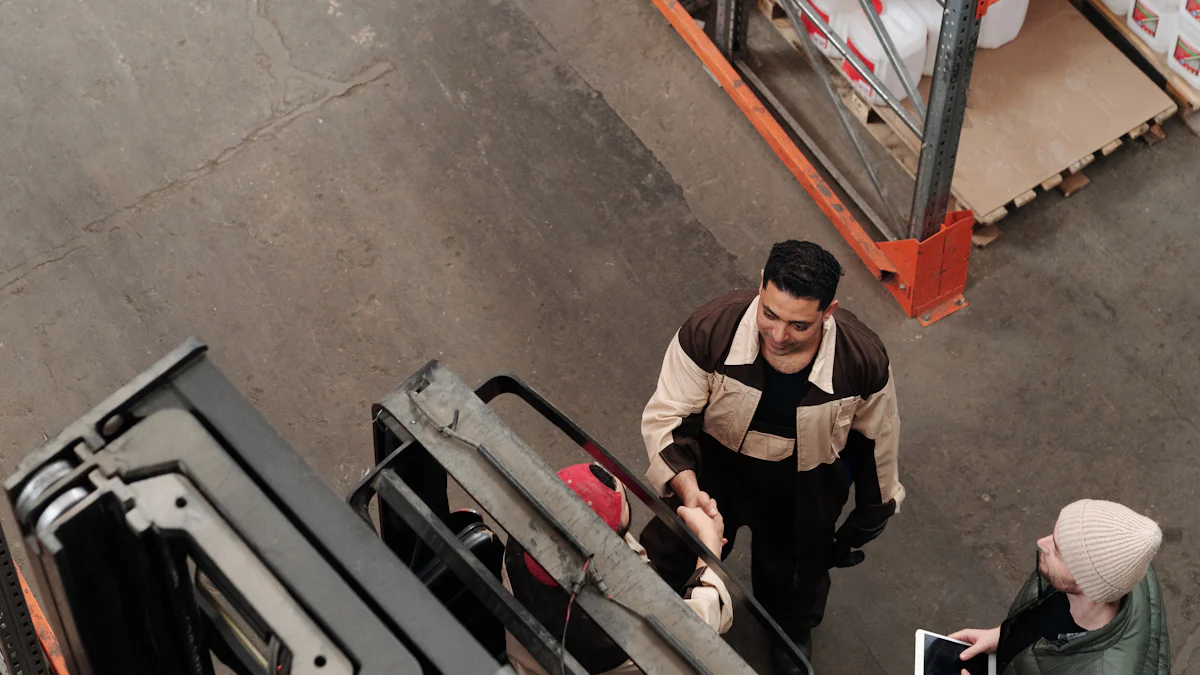
Pallet Jack Won’t Move
Checking the Accelerator
Inspecting the accelerator is essential when troubleshooting a pallet jack that won’t move. Begin by examining the accelerator pedal for any signs of damage or obstruction. Ensure that the pedal moves freely without any resistance, as this component plays a crucial role in controlling the forward and backward movement of the pallet jack. By checking the accelerator regularly, operators can identify potential issues early on and address them promptly to restore optimal functionality.
Inspecting the Hydraulic Lift
When faced with a pallet jack that refuses to move, it is vital to inspect the hydraulic lift system thoroughly. Start by examining the hydraulic fluid levels in the reservoir to ensure they are within the recommended range. Low fluid levels can impede the lifting mechanism’s operation, causing the pallet jack to malfunction. Additionally, check for any leaks or damaged hydraulic lines that may affect the system’s pressure and performance. By conducting regular inspections of the hydraulic lift components, operators can prevent potential breakdowns and ensure smooth operation.
Pallet Jack Won’t Go Down
Releasing the Valve
If a pallet jack is experiencing difficulty lowering its forks, releasing the valve is a crucial troubleshooting step. Operators should locate the release valve near the hydraulic pump and gradually turn it counterclockwise to release pressure from the system. This action allows hydraulic fluid to flow back into the reservoir, enabling the forks to descend smoothly. By releasing the valve correctly, operators can troubleshoot issues related to fork movement and maintain operational efficiency.
Using Another Jack
In situations where a pallet jack remains stuck in an elevated position and won’t go down despite troubleshooting efforts, using another jack for assistance is recommended. Positioning a secondary jack or forklift behind the stuck pallet jack’s wheels provides additional support for lowering it safely. Apply gradual pressure on the forks or utilize external force to coax them into descending position. By leveraging another jack’s assistance strategically, operators can overcome challenges related to a non-responsive pallet jack and resume normal operations promptly.
- To ensure the longevity and optimal performance of your pallet jack, it is essential to recap the repair steps diligently.
- Emphasize the significance of regular maintenance to prevent unexpected breakdowns and maintain operational efficiency.
- Seeking professional help for complex issues can provide expert solutions tailored to your specific needs, ensuring seamless operations and cost savings in the long run.
By understanding the importance of proper maintenance and repair techniques, businesses can boost productivity, enhance safety standards, and achieve significant cost savings over time. Utilizing maintenance management software for scheduled servicing can keep equipment in prime condition, reducing downtime and maximizing operational output. Remember, investing in professional servicing tailored to your requirements is key to keeping your pallet trucks running smoothly and efficiently.
Post time: Jun-05-2024