Manual pallet jack safety is paramount in any workplace to prevent accidents and injuries. Understanding the risks associated with manual pallet jacks is crucial for ensuring a safe working environment. By following key safety tips, employees can mitigate hazards effectively. Zoomsun‘s unwavering dedication to safety underscores the importance of prioritizing employee well-being through proper training and adherence to safety protocols. Displaying a manual pallet jack safety poster can further reinforce these safety measures and remind employees of best practices.
Importance of Safety Training
In the realm of workplace safety, safety training stands as a cornerstone for ensuring the well-being of employees. Understanding the potential hazards that come with operating manual pallet jacks is paramount to creating a secure work environment. By recognizing and addressing these risks head-on, organizations can significantly reduce the likelihood of accidents and injuries.
Understanding Hazards
Common Risks
- Lack of proper training can lead to accidents and injuries.
- Overloading the pallet jack beyond its capacity poses a significant risk.
- Inadequate maintenance may result in malfunctioning equipment.
- Ignoring safety protocols increases the chances of workplace incidents.
Preventive Measures
- Conduct regular safety training sessions to educate employees on best practices.
- Implement strict guidelines on load capacity to prevent overloading.
- Establish routine maintenance checks to ensure equipment is in optimal condition.
- Enforce safety procedures consistently to promote a culture of caution.
Safe Work Practices
Rules of the Road
- Always yield to pedestrians and other equipment in shared spaces.
- Observe speed limits and maintain control while maneuvering pallet jacks.
- Use designated pathways and avoid shortcuts that compromise safety.
Training Programs
- Develop comprehensive safety training programs tailored to different job roles.
- Utilize interactive learning tools such as simulations for practical understanding.
- Offer refresher courses periodically to reinforce safety protocols.
Manual Pallet Jack Safety Poster
- Display clear illustrations demonstrating safe operating techniques.
- Include warning signs for common hazards like slippery surfaces or blind spots.
Placement and Accessibility
- Position safety posters strategically in high-traffic areas for maximum visibility.
- Ensure posters are well-lit and free from obstructions for easy reference by employees.
By prioritizing safety training, organizations equip their workforce with the knowledge and skills necessary to navigate potential risks effectively, fostering a culture of vigilance and responsibility within the workplace.
Proper Use and Handling
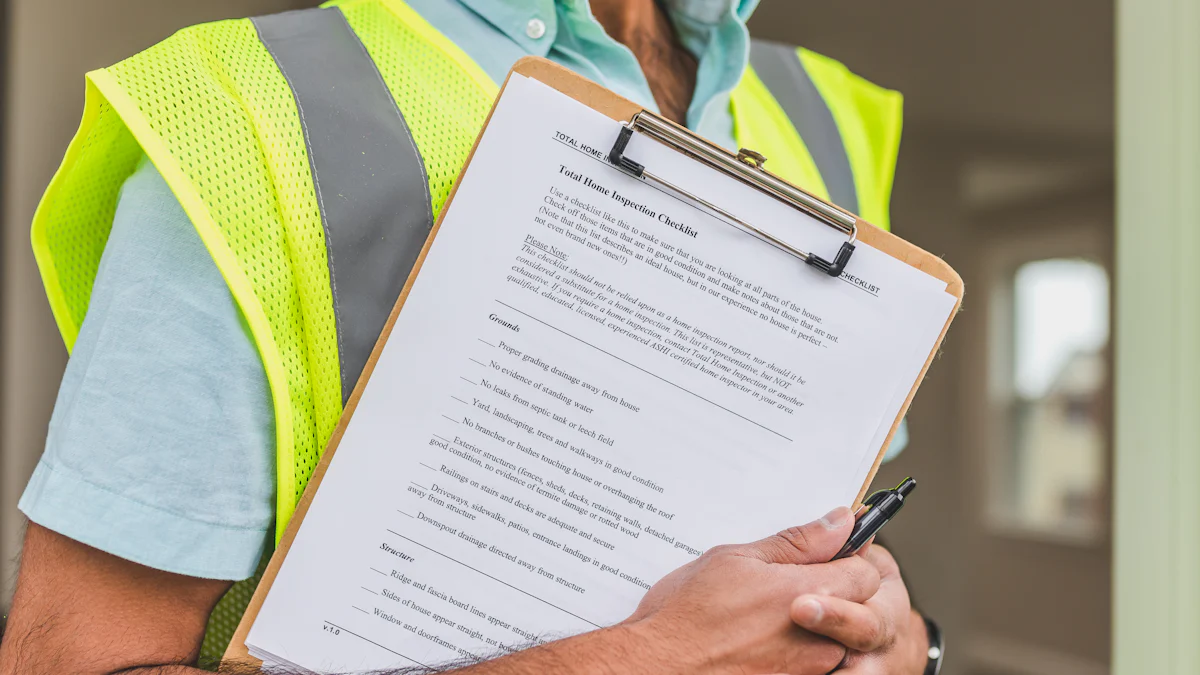
Operating Techniques
When operating a manual pallet jack, it is essential to understand the nuances of pushing versus pulling and maneuvering in tight spaces. These techniques play a crucial role in ensuring efficient material handling operations.
Pushing vs. Pulling
- Pushing the manual pallet jack is generally recommended over pulling to minimize strain on the operator’s body. By pushing the jack, employees can utilize their body weight more effectively, reducing the risk of injuries associated with pulling heavy loads.
- Pulling, on the other hand, can lead to muscle strains and potential accidents if not executed properly. Operators should be cautious when pulling a loaded pallet jack to avoid sudden movements that could result in loss of control.
Maneuvering in Tight Spaces
- Maneuvering a manual pallet jack in confined spaces requires precision and spatial awareness. Operators must navigate corners and narrow aisles carefully to prevent collisions with obstacles or other equipment.
- Utilizing proper hand placement on the handle and maintaining clear lines of sight are essential for safe navigation in tight spaces. By adopting smooth steering techniques, operators can enhance operational efficiency while minimizing the risk of accidents.
Load Management
Efficient load management is key to maximizing the utility of manual pallet jacks while ensuring workplace safety. Balancing loads correctly and avoiding overloading are fundamental principles that every operator should adhere to.
Balancing Loads
- When loading items onto a pallet jack, it is crucial to distribute weight evenly across the platform. Unevenly distributed loads can lead to instability during transport, increasing the likelihood of accidents or product damage.
- Properly securing loads with straps or tie-downs can further enhance load stability and prevent shifting during transportation. By prioritizing load balance, operators contribute to a safer working environment for themselves and their colleagues.
Avoiding Overloading
- Exceeding the manufacturer’s specified load capacity poses significant risks not only to personnel but also to equipment integrity. Operators must be vigilant in adhering to weight limits outlined by the manufacturer for each specific manual pallet jack model.
- Regular checks on load weights before transportation are essential practices that help prevent overloading incidents. By staying within designated load capacities, operators uphold safety standards while prolonging the lifespan of equipment.
Maintenance and Inspection
Routine maintenance and thorough inspections are integral components of manual pallet jack safety protocols. By conducting regular checks and promptly addressing any issues identified, organizations can sustain operational efficiency while safeguarding employee well-being.
Regular Checks
- Scheduled inspections should encompass critical components such as wheels, handles, forks, and hydraulic systems. Any signs of wear or damage should be addressed immediately to prevent equipment failure during operation.
- Lubricating moving parts regularly ensures smooth functionality and prolongs the lifespan of manual pallet jacks. Routine maintenance tasks contribute significantly to overall equipment reliability and performance consistency.
Reporting Issues
- Encouraging employees to report any malfunctions or abnormalities observed during operation fosters a proactive approach towards equipment safety. Timely reporting enables swift resolution of issues before they escalate into serious hazards.
- Establishing clear communication channels for reporting maintenance concerns empowers employees to contribute actively towards maintaining a safe working environment. By prioritizing transparency and accountability, organizations promote a culture of shared responsibility for workplace safety.
Personal Protective Equipment (PPE)
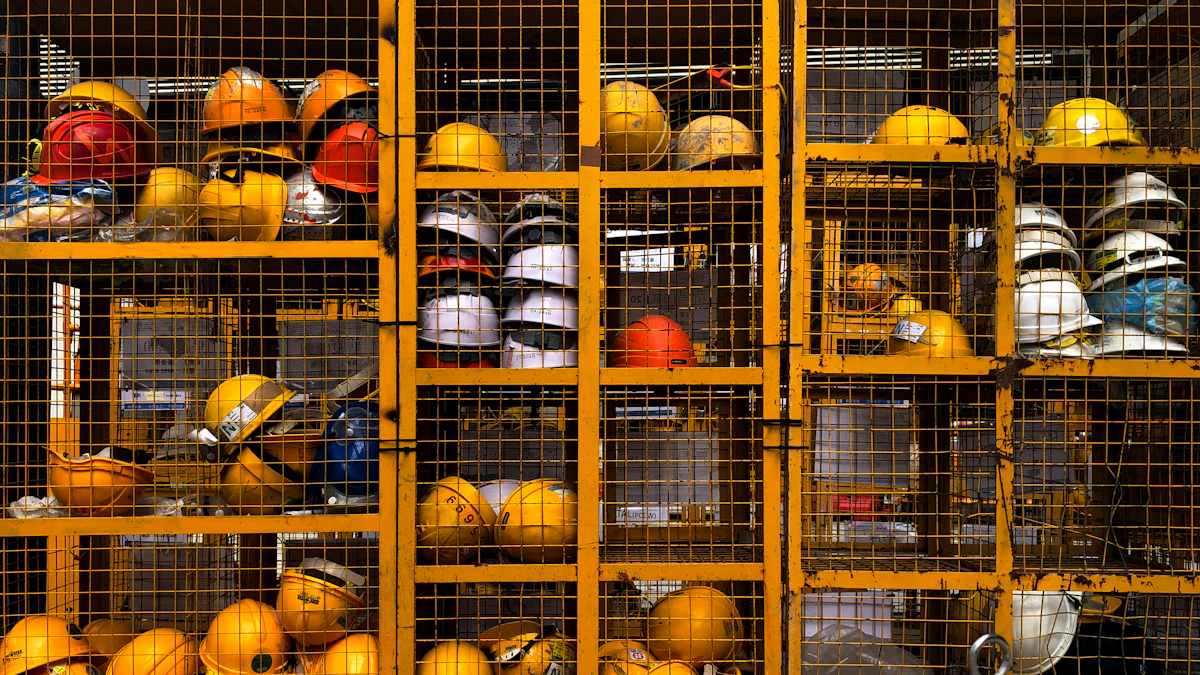
Importance of PPE
Types of PPE
- Footwear: Sturdy shoes with slip-resistant soles are essential to prevent slips and falls in the workplace. Steel-toed boots offer additional protection against heavy objects.
- Gloves: Proper gloves protect hands from cuts, abrasions, and chemicals. Choose gloves that fit well and provide adequate dexterity for handling materials.
- High Visibility Clothing: Brightly colored or reflective clothing enhances visibility, reducing the risk of collisions in busy work environments.
- Eye Protection: Safety glasses or goggles shield the eyes from debris, dust, and other hazards. Ensure eye protection meets industry standards for impact resistance.
- Head Gear: Helmets or hard hats safeguard against head injuries caused by falling objects or bumps in low-clearance areas.
Proper Usage
- Select the appropriate PPE based on the specific hazards present in your work environment.
- Inspect PPE before each use to ensure it is in good condition without any visible damage.
- Wear PPE consistently whenever engaging in tasks that require protective equipment.
- Follow manufacturer instructions for proper care, maintenance, and replacement of PPE items.
- Store PPE in designated areas to prevent damage and contamination when not in use.
Employer Responsibilities
Providing PPE
Employers have a legal obligation to provide employees with suitable Personal Protective Equipment as per OSHA regulations. This includes:
- Offering a range of PPE options tailored to different job roles and hazards present.
- Ensuring that all provided PPE meets industry standards for safety and performance.
- Regularly assessing the effectiveness of existing PPE and updating as needed to maintain optimal protection levels.
Ensuring Compliance
- Conduct regular training sessions on the importance of wearing PPE correctly and consistently.
- Enforce strict policies mandating the use of appropriate PPE for designated tasks.
- Monitor compliance with PPE guidelines through routine inspections and feedback mechanisms.
- Address any non-compliance issues promptly through corrective actions or additional training initiatives.
- Encourage open communication regarding any concerns or suggestions related to PPE usage among employees.
By prioritizing the provision and proper utilization of Personal Protective Equipment, employers demonstrate their commitment to creating a safe working environment where employee well-being is paramount. Adhering to established safety protocols not only safeguards individuals from potential risks but also fosters a culture of responsibility and vigilance towards workplace safety practices.
Load Capacity and Limits
Manufacturer’s Guidelines
Reading Load Capacity
- Always refer to the manufacturer’s guidelines for the specific load capacity of the manual pallet jack. This information is crucial as it ensures that operators do not exceed the maximum weight limit recommended by the manufacturer.
- The load capacity, typically indicated on a label or plate affixed to the pallet jack, specifies the maximum weight that can be safely transported. By adhering to this limit, operators mitigate the risk of overloading and maintain operational safety.
- Understanding and interpreting load capacity information is essential for safe material handling practices. Operators should familiarize themselves with these guidelines to prevent accidents and ensure workplace safety.
Adhering to Limits
- Adhering strictly to the manufacturer’s specified load limits is imperative for safe operation. Exceeding these limits can compromise equipment integrity and pose significant risks to both operators and bystanders.
- By following load limits diligently, operators uphold safety standards and contribute to a secure working environment. Regular checks on load weights before transportation help prevent overloading incidents, promoting efficient and accident-free material handling operations.
- Manufacturers design manual pallet jacks with specific load capacities based on structural considerations and operational safety. Respecting these limits is fundamental to preventing accidents, maintaining equipment longevity, and safeguarding personnel in the workplace.
Safe Loading Practices
Distributing Weight Evenly
- When loading items onto a manual pallet jack, ensure that weight distribution is even across the platform. Unevenly distributed loads can lead to instability during transport, increasing the risk of accidents or product damage.
- Properly balancing loads minimizes the likelihood of tipping or loss of control while maneuvering the pallet jack. By distributing weight evenly, operators enhance stability and reduce potential hazards associated with unevenly loaded pallets.
- Implementing safe loading practices not only protects personnel from injuries but also preserves product integrity during transportation. Prioritizing even weight distribution contributes to efficient material handling processes while upholding workplace safety standards.
Avoiding Overhead Obstructions
- Operators should remain vigilant for overhead obstructions when maneuvering loaded pallet jacks. Awareness of ceiling heights, door frames, or hanging obstacles is crucial to prevent collisions that could endanger personnel or damage goods.
- Clear pathways from any overhead barriers before transporting loads with a manual pallet jack. Maintaining an unobstructed vertical clearance minimizes risks associated with accidental impacts or entanglements during material handling operations.
- Avoiding overhead obstructions requires attentiveness and proactive hazard identification by operators. By exercising caution and foresight in navigating workspaces, employees contribute to a safer environment conducive to efficient and incident-free material handling activities.
- Summarize the essential safety tips discussed throughout the blog to reinforce a culture of workplace safety.
- Highlight the critical role of training and Personal Protective Equipment (PPE) in mitigating risks and ensuring employee well-being.
- Encourage proactive implementation of safety measures to enhance operational efficiency and reduce accidents.
- Recognize Zoomsun’s commitment to promoting workplace safety through their quality material handling equipment.
Post time: May-29-2024