Maintaining pallet jacks is crucial for workplace safety and efficiency. Regular upkeep not only prevents unexpected breakdowns but also prolongs the lifespan of the equipment. Identifying wear and tear early on, especially on the wheels, is essential to ensure a safe working environment. According to industry insights, neglecting maintenance can lead to severe consequences, such as major injuries or even fatalities. Therefore, understanding how to fix a pallet jack and the common problems that arise with pallet jacks and their solutions is key to avoiding costly repairs and ensuring smooth operations.
Common Problems Overview
Overview of Pallet Jack Issues
Regular maintenance is crucial for the safety, performance, and longevity of pallet jacks. Proper upkeep can prevent accidents, injuries, and costly damage to the equipment. By conducting regular maintenance checks, businesses can ensure the smooth operation of their pallet jacks and avoid unexpected breakdowns. This proactive approach not only enhances workplace safety but also contributes to the overall efficiency of operations.
When it comes to pallet jack issues, early identification is key. By recognizing common problems in their initial stages, operators can address them promptly before they escalate into more significant issues. For instance, noticing signs of wear and tear on the wheels or hydraulic system can indicate a need for immediate attention. Identifying these problems early on allows for timely intervention and prevents potential disruptions in workflow.
How to Fix a Pallet Jack
Addressing pallet jack problems effectively requires following general troubleshooting steps. These steps involve systematically diagnosing the issue, identifying the root cause, and implementing appropriate solutions. By approaching problem-solving in a structured manner, operators can efficiently resolve issues and restore the functionality of their equipment.
Proper diagnosis is a critical aspect of fixing pallet jack problems. Before attempting any repairs or adjustments, it is essential to accurately pinpoint the source of the issue. This may involve inspecting various components such as the hydraulic system, forks, or lubrication points to identify any anomalies. Through thorough diagnosis, operators can ensure that they are addressing the underlying problem rather than just its symptoms.
Lubrication Issues
Ensuring smooth operation through lubrication minimizes friction between moving parts, extending the lifespan of your equipment. Proper lubrication plays a crucial role in maintaining the functionality of your Pallet Jack. Lubricating moving parts such as hinges and joints ensures smooth operation and reduces wear and tear on critical components.
Poor Lubrication
Causes of Poor Lubrication
- Neglecting regular maintenance schedules.
- Using incorrect or low-quality lubricants.
- Environmental factors like dust and debris accumulation hindering proper lubrication.
Solutions for Lubrication Problems
- Follow manufacturer guidelines for lubrication frequency.
- Use high-quality, recommended lubricants suitable for Pallet Jacks.
- Regularly clean moving parts before applying lubricant to ensure effectiveness.
Preventive Measures
Regular Lubrication Schedule
- Create a maintenance calendar for timely lubrication intervals.
- Inspect moving parts routinely to identify any signs of inadequate lubrication.
Recommended Lubricants
- Utilize lithium-based greases for optimal performance.
- Consider synthetic oils for enhanced durability and protection against wear.
Lubricating your Pallet Jack’s moving parts is an important task that requires some preparation and caution. Firstly, clean the moving parts with a cloth or brush to remove dirt, dust, or debris. Then, use a suitable tool such as a grease gun or spray nozzle to apply the lubricant to the moving parts. Focus on the most exposed parts such as wheels, bearings, axles, chains, forks, and hydraulic pump.
Afterward, wipe off any excess lubricant with a cloth or paper towel. Finally, test your Pallet Jack’s operation and check for any abnormalities like squeaking, jamming, or leaking. By following these best practices you can ensure that your Pallet Jack is well-lubricated and functioning smoothly.
Regularly lubricate all moving parts according to the manufacturer’s instructions; this helps reduce friction and wear while extending the lifespan of your equipment significantly.
Hydraulic System Problems
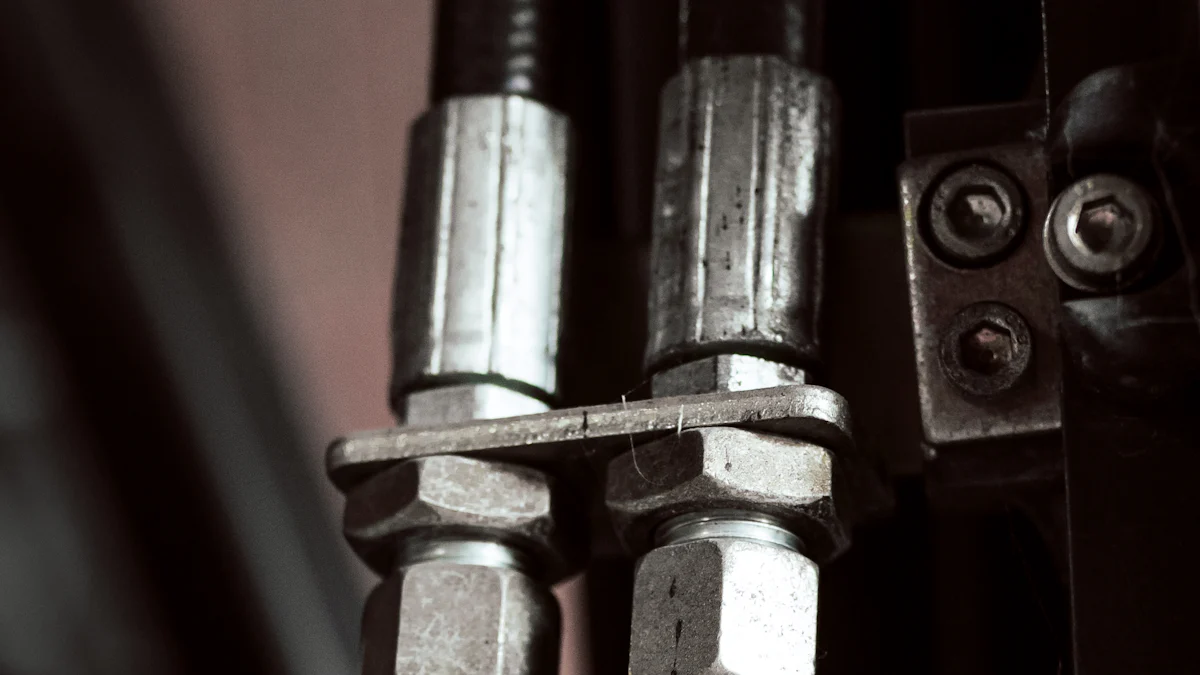
Trapped Air in Hydraulic System
Implementing troubleshooting steps to diagnose issues with the lifting mechanism is essential for identifying root causes and implementing effective solutions. Common troubleshooting measures include checking hydraulic fluid levels, inspecting control valves, and testing the pump assembly for proper functioning.
- Causes of Trapped Air:
- Neglecting regular maintenance schedules can lead to air getting trapped in the hydraulic system.
- Improper bleeding of the system after maintenance or repairs can result in air pockets.
- Damaged seals or connections may allow air to enter the hydraulic system.
- Solutions for Trapped Air:
- Bleed the hydraulic system properly by following manufacturer guidelines.
- Use a suitable bleeding tool to remove trapped air from the system effectively.
- Inspect all seals and connections for any signs of damage and replace them if necessary.
Damaged O-Rings
The hydraulic system is responsible for the lifting and lowering operations of the jack. Check for any leaks or damages. If you notice any issues, get them repaired immediately.
- Causes of Damaged O-Rings:
- Continuous usage without proper maintenance can cause wear and tear on O-rings.
- Exposure to harsh environmental conditions like extreme temperatures or chemicals can deteriorate O-rings.
- Incorrect installation or over-tightening of components may damage O-rings over time.
- Solutions for Damaged O-Rings:
- Cut power to the hydraulic system before attempting any repairs on damaged O-rings.
- Carefully remove the damaged O-ring using appropriate tools without causing further harm.
- Install a new O-ring of the correct size and material, ensuring a proper seal to prevent future issues.
Inspecting the hydraulic unit regularly is crucial to identify potential problems early on. By addressing trapped air and damaged O-rings promptly, operators can maintain the optimal performance of their pallet jacks and prevent more significant issues from arising. Remember that proper maintenance not only ensures safety but also extends the lifespan of your equipment, contributing to a more efficient workplace environment.
Fork Misalignment
When pallet jacks exhibit fork misalignment, it can significantly impact their operational efficiency. Continuous usage issues are a common cause of this problem, leading to uneven forks that make it challenging to maneuver pallets effectively. The misalignment not only affects the stability of the load but also poses safety risks in the workplace. Users may struggle to position the forks correctly under pallets, resulting in potential accidents or damage to goods.
To address fork misalignment, operators can consider realigning forks as a practical solution. By adjusting the forks to ensure they are level and parallel, users can improve the functionality of the pallet jack and enhance load-bearing capabilities. Proper alignment not only facilitates smoother pallet insertion and extraction but also minimizes the risk of accidents associated with unstable loads.
Solutions for Fork Misalignment
Realigning Forks
- Inspect Fork Alignment: Begin by examining the current alignment of the forks to identify any discrepancies or tilts.
- Adjust Fork Position: Using appropriate tools, carefully realign the forks to ensure they are parallel and at an equal height.
- Test Functionality: After realignment, test the pallet jack by inserting it under a standard pallet to verify that both forks slide in smoothly.
- Fine-Tune Alignment: Make minor adjustments if necessary to achieve optimal alignment for efficient pallet handling.
Preventive Measures
- Regular Inspections: Conduct routine checks on fork alignment to detect any signs of misalignment early on.
- Operator Training: Provide training to operators on proper handling techniques and how to identify signs of fork misalignment.
- Maintenance Records: Keep detailed records of maintenance activities, including fork realignment procedures and dates.
By implementing these solutions and preventive measures, businesses can mitigate the risks associated with fork misalignment in their pallet jacks. Ensuring that forks are properly aligned not only enhances operational safety but also contributes to overall productivity by reducing downtime caused by handling issues.
Oil Pump Issues
Common Oil Pump Problems
Causes of Oil Pump Issues
- Neglecting regular oil pump maintenance can lead to a decrease in pump efficiency and performance over time.
- Using the wrong type of hydraulic oil or failing to check oil levels regularly may result in inadequate lubrication and cause pump malfunctions.
- Environmental factors like dust, debris, or moisture contamination can contribute to oil pump problems by affecting the quality of the hydraulic fluid.
Solutions for Oil Pump Problems
- Regular Oil Pump Maintenance:
- Implement routine checks on the oil pump, including inspecting for leaks, testing pressure levels, and ensuring proper oil circulation.
- Clean the pump components regularly to prevent debris buildup and maintain optimal functionality.
- Replace worn-out parts promptly to prevent further damage to the oil pump system.
- Signs of Oil Pump Failure:
- Monitor for unusual noises coming from the pump, such as grinding or whining sounds, which may indicate internal issues.
- Check for visible leaks or drips around the pump assembly that could signal a potential malfunction in the system.
- Observe any changes in hydraulic fluid color or consistency, as discoloration or contamination may signify underlying problems with the oil pump.
Regular maintenance is essential for preserving the integrity and performance of pallet jack components. By adhering to recommended maintenance practices and promptly addressing any identified issues with the oil pump system, operators can ensure smooth operations and extend the lifespan of their equipment. Remember that proactive care not only enhances safety but also contributes to operational efficiency in warehouse environments.
Regular maintenance is crucial for ensuring optimal performance and longevity of pallet jacks. Implementing a regular service and maintenance plan reduces the risk of operational downtime and ensures equipment performance at its best. Regular preventive maintenance helps in preventing unexpected breakdowns and saving time and money in the long run. By conducting routine maintenance checks, businesses can identify and address minor issues before they escalate into major problems, reducing the risk of costly repairs or replacement. Remember, proactive care not only enhances safety but also contributes to operational efficiency in warehouse environments.
Post time: Jun-14-2024